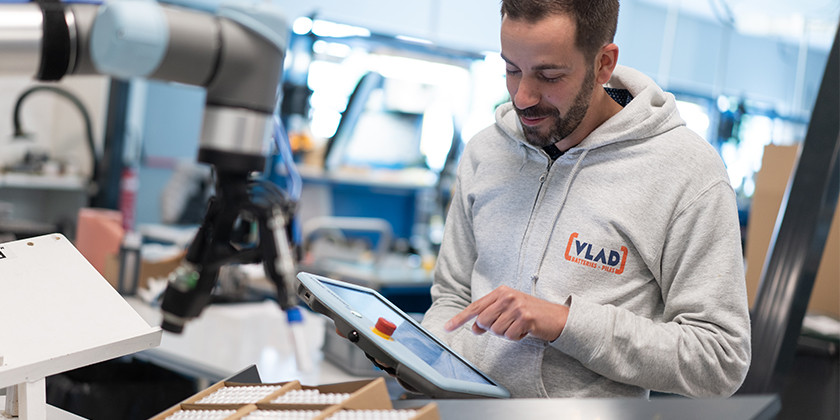
In the midst of a health crisis, the five collaborative robots, integrated on the company's site in Parcay-Meslay for welding, bonding and assembly applications, have also enabled the company to improve the working conditions of its operators and reduce the error rate...
Founded in 1985, VLAD is a historical reference player in the industrial and medical sector in France. The company specializes in the design and manufacture of high-tech medical cells and batteries for hospitals and care centers. In March 2020, at the very beginning of the Covid-19 crisis, the group found itself faced with an explosion in demand for batteries for respirators that it manufactures as original equipment.
In parallel, the company had started in 2019 to evolve its production tool towards Industry 4.0, including the automation of certain physically strenuous tasks with low added value. The production site, which has 75 employees, produces 150,000 high-quality batteries per year, in small series, for no less than 1,500 different references.
A technological turning point
For VLAD, the onset of the crisis and the increase in demand served as a lever to accelerate its modernization.
An essential component of Industry 4.0, cobotics was to enable VLAD to meet the following objectives:
- Reduce repetitive tasks with low added value for operators;
- Minimize the risk of errors within the line;
- Improve productivity on tasks requiring high precision;
- Master and modulate robotic lines in total independence.
After several months of reflection, the choice fell on Universal Robots COBOTS UR5e and UR10e, integrated with the help of HMi-MBS, distributor of Universal Robots. The management sought above all that cobots were tools serving as assets for operators, without belittling their work. VLAD has also chosen to train in the mastery of cobots to develop automated lines by itself.
The first production line, used to build battery packs, has three robots. The first cobot supports a Pick & Place application to take cells out of suppliers' boxes; the second a bonding application to assemble cells of these battery packs and the last welds them together. The second production line follows a similar pattern, with a Pick & Place cobot and a welding cobot.
Operations are monitored and controlled remotely by operators, who can focus on higher value-added tasks such as finishing battery packs or quality inspection.
Improvements on all fronts
The partial automation of production lines with cobots has brought many benefits to VLAD. In addition to reducing employees' MSDs by sparing them from performing repetitive tasks, the cobots have enabled the company to reduce cell positioning errors (including reverse polarity errors) as well as glue consumption.
VLAD also increased its productivity, +10% overall in 2020, despite the crisis, and tripled its production of batteries for respirators. « The cobots helped us support the necessary production capacities in March and April 2020. Without them, we wouldn't have been able to make the batteries to power the ventilators hospitals needed. "explains Damien Chaumette, Systems Manager at VLAD.
On the operator side, the cobots were well received. « There were concerns " admits Damien Chaumette. To remove these doubts, we involved our collaborators from the beginning of the project, which made it possible to demystify the cobot, to explain its role and what it was going to do. The experience was part of something playful. Considered as a support, the cobot took away redundant, and sometimes painful, tasks. Their work has become more qualitative: control, supervision... and there are always manual tasks that are carried out, which now reveal their full value."
With this cobotic cell, VLAD can launch different production series as a result without adjustments on the robots or tool changes. For the future, the company is considering extending this automation to other production lines, in parallel with the modernization of its existing tools.